Mastering Plastic Injection Mold Tooling: Your Guide to Precision Manufacturing
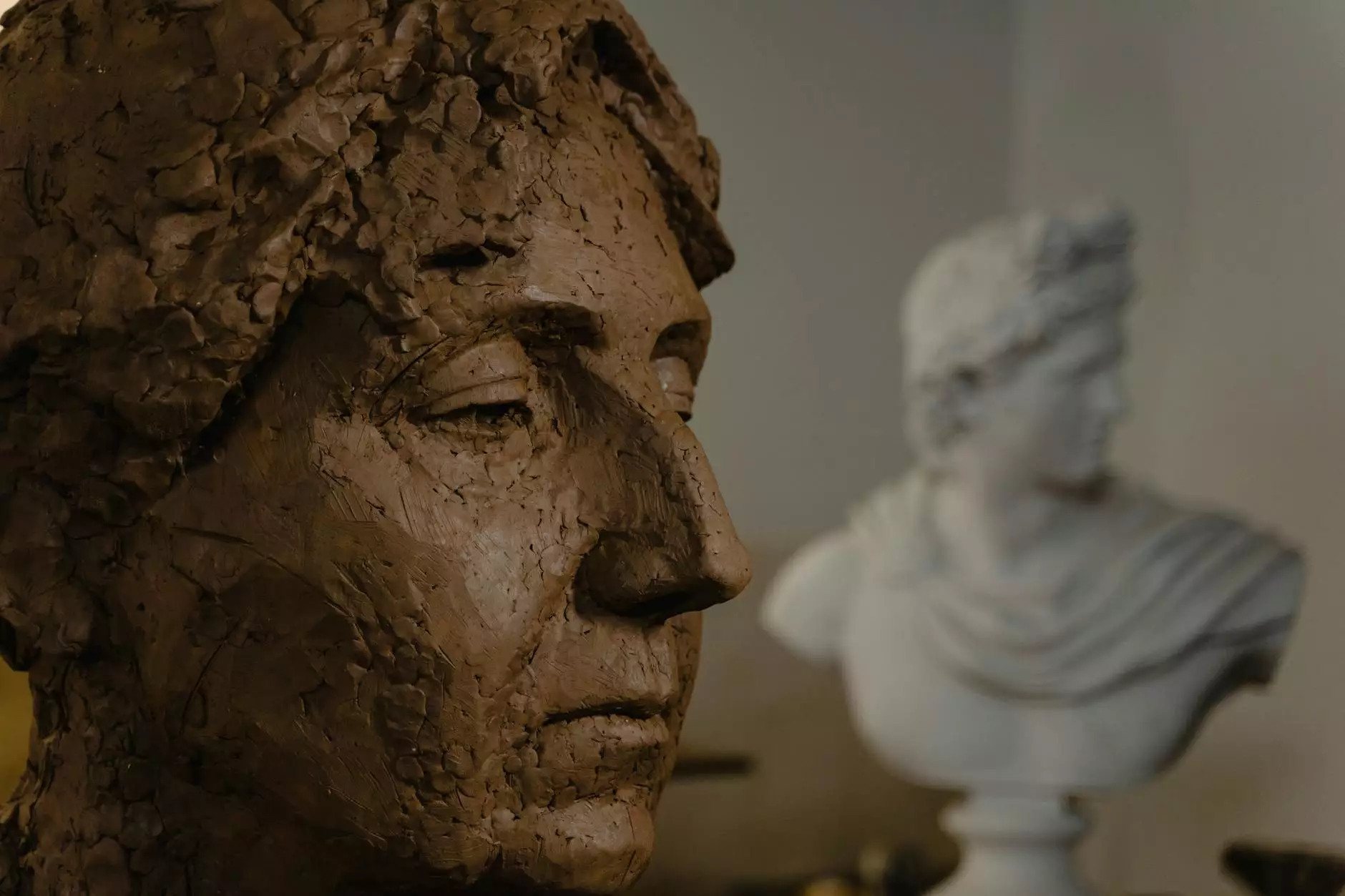
Understanding Plastic Injection Mold Tooling
Plastic injection mold tooling is a critical component in the manufacturing industry, representing the process where molten plastic is injected into a mold to create various parts and products. This intricate procedure allows for the mass production of high-quality components, which are essential in diverse industries, from automotive to consumer goods. The effectiveness of this method depends significantly on the design and quality of the tooling involved.
The Significance of Mold Tooling in Manufacturing
Mold tooling is central to producing intricately designed and durable plastic parts. The precision and efficiency of plastic injection mold tooling directly influence production speed and part quality. This process not only offers consistent results but also reduces material waste, making it an eco-friendly manufacturing choice.
Key Benefits of Plastic Injection Mold Tooling
- High Efficiency: Once a mold is created, it can produce thousands of identical parts with minimal downtime.
- Cost-Effectiveness: Though the initial investment is high, the long-term savings on production costs are significant due to reduced cycle times and minimized material waste.
- Design Flexibility: Allows for complex designs and precision engineering that manual processes cannot achieve.
- Material Variety:Compatible with numerous thermoplastics and thermosetting polymers, allowing manufacturers to select materials based on performance requirements.
The Process of Plastic Injection Mold Tooling
The process of plastic injection mold tooling involves several key stages:
- Design Specification: Before any tooling can begin, manufacturers must define specifications based on product requirements.
- Mold Design: Expert mold designers create CAD (Computer-Aided Design) models of the mold, taking into account factors that affect functionality and efficiency.
- Mold Fabrication: Using advanced machining techniques, molds are manufactured from durable materials such as steel or aluminum.
- Mold Testing: Before full-scale production, molds undergo testing to ensure they perform as expected under real-world conditions.
- Production: Once validated, the molds go into full production, where molten plastic is injected, cooled, and ejected to create the final product.
Types of Injection Molds
There are several types of molds used in plastic injection mold tooling, each tailored to different needs:
1. Single Cavity Molds
This mold produces one part per cycle and is typically used for simple projects or lower volume production runs.
2. Multi Cavity Molds
Designed to produce multiple parts in one cycle, these molds are ideal for high-volume production, improving efficiency and reducing costs.
3. Family Molds
Family molds are capable of producing different parts in a single mold, allowing manufacturers to streamline production when multiple components are needed.
4. Hot Runner Molds
In hot runner molds, a heated system remains in contact with the plastic as it travels through the mold, reducing waste and allowing for faster production cycles.
Materials Used in Mold Tooling
Plastic injection mold tooling requires robust materials to withstand the high pressures and temperatures involved in the molding process. Commonly used materials include:
- Steel: Known for its strength and durability, making it suitable for high-production runs.
- Aluminum: Lightweight and easier to machine; often used for prototyping and lower volume projects.
- Bronze: Sometimes incorporated for specific components due to its excellent wear resistance.
Maintaining Injection Molds
The longevity and efficiency of plastic injection mold tooling can be significantly influenced by proper maintenance practices. Here are some tips:
1. Regular Cleaning
Molds should be cleaned frequently to prevent residue buildup, which can lead to defects in the final product.
2. Inspections
Regular inspections for wear and tear can help in early identification of maintenance needs before they interfere with production.
3. Lubrication
Using appropriate lubricants can reduce friction and prolong the life of moving components within the mold.
The Future of Plastic Injection Mold Tooling
As technology evolves, so does the field of plastic injection mold tooling. Innovations such as:
- 3D Printing: Enables rapid prototyping, allowing for faster iterations in mold design.
- Automation: Robotic systems are increasingly integrated into the injection process, improving efficiency and reducing labor costs.
- Smart Manufacturing: The use of IoT (Internet of Things) technology helps track mold performance and predict maintenance needs.
Conclusion
In summary, plastic injection mold tooling is a cornerstone of modern manufacturing processes. Understanding its function, benefits, and ongoing advancements is essential for businesses involved in production, whether they are small startups or large-scale operations. By investing in high-quality tooling and adopting best practices for maintenance and innovation, manufacturers can enhance their productivity and deliver superior products to the market.
For more detailed insights into plastic injection mold tooling and its applications, visit deepmould.net.